次に進む
1つ戻る
- 1.パンタグラフ
- 2.車両の外寸
- 3.鉄道車両の軸重と材質
- 4.車体外側の標示
- 5.ETCS(列車運行システム)
- 6.オーバーラップと信号の変化
- 7.連結装置
- 8.脱出窓
- 9.レールの接地/非接地
- 10.ATCの速度照査パターンの引き方
- 11.電磁吸着ブレーキ
- 12.分岐器の鎖錠
- 13.デジタルモデリング・BIM・UICリーフレット
- 14.軌道構造
- 15.軌道構造・人材育成
- 16.接着・溶接認証
- 17.「速度信号」「予告信号」が必要な理由
- 18.速度超過検出
- 19.異相区分切替セクション
- 20.波動伝搬速度[架線の構造]
- 21.サードレールの活用
- 22.車両材料による火災対策
- 23.鉄道運転免許
- 24.プラットホームの高さ・ドア高さとドアの大きさ
- 25.車両のドア構造
- 26.5G対応無線式信号(FRMCS)
- 27.高速鉄道線のトンネルの断面積
- 28.列車の分類
- 29.民営化された国鉄路線(工事中)
- 30.行路表の配布者
- 31.オープンアクセスは強制開放
- 32.客室の座席配置(工事中)
- 33.列車位置把握(工事中)
- 34.高速鉄道の在来線線路走行
- 35.メンテナンス
- 36.車両の堅牢さ
- .日欧の違い まとめ
目次
メンテナンス戦略
故障を許容する度合の違い
このサイトでは、メンテナンスについては欧州の車両保守認証制度(ECM)と、日本における鉄道車両のメンテナンス周期について紹介します。
ここでは、それらのメンテナンスの背景にある、どのような思想で故障等(Failure※)を防ぐか、という戦略(思想)の違いについてご紹介し、その、日欧比較をいたします。
※所定の機能が発揮できないことを、ここでは「故障」と言うことにしております。
なお、メンテナンス作業の範囲については日欧ではかなり差があります。例えば、「技術的な清掃(フィルター掃除など)」以外の内装の清掃作業は、日本ではメンテンナンスに含まれていませんがヨーロッパでは含まれます。こうした作業内容の違いについてはここでは触れません。
メンテナンスの種類
メンテナンスには、様々なコンポーネントに対して点検・測定・交換・転削等多くのレベルの作業がありますが、その作業を行う背景にある、故障による悪影響を防ぐ考え方は以下の3つに分けることができます。
- @予防保全 :一定期間・一定距離を定めて、それに達した場合に交換する。
- A状態監視保全:状態監視を行い、技術的に定めた閾値に達した場合に交換する。
- B事後保全 :故障等が顕在化した場合に交換・修理する。
卑近な例を挙げると、例えば家庭用温水便座はメーカーがxx年で交換するようにと推奨しております。これを本当にxx年で交換する方針は、@予防保全 の考え方です。何の異変も無くても交換するわけですが、メーカーの推奨に沿っていますから、事故が起きる可能性は最も低いですね。
次に、軽微な異変などの予兆事象から故障が近いことを察知して交換するのが、Aの状態監視保全です。
最後に、故障してから交換するのがBの事後保全です。トイレ1つしかない場合、修理/交換するまでの間困りますから、これはまずいですよね。
日本の場合
上述の3種類のメンテナンス戦略について、日本では安全性に関わるものは@予防保全 により交換されています。もっとも、ワイパーが3つあるとか予備のパンタグラフがあるような、1つ2つ壊れても問題が無い(これを冗長系と呼びます)システムについては別です。
予防保全は、壊れていないのにある決められた時間・距離を使用したら新品に交換してしまいますので、コストがかかることが難点です。そのため最近では、発達したIT技術を利用してより賢く交換するA状態監視保全 が取り入れられています。JRさんでは新保全体系と呼ぶものもこの一つで、より合理的に故障する前に交換をする時期を設定しておく、より賢くて財布に優しい方法です。
3種類の中では、この状態監視保全が最も好ましそうにみえますが、状態監視技術の進展にもかかわらず、まだまだ難しい点も多いです。
たとえば、故障の予兆(Potential Failure)が無く突然壊れる特性の製品(電子部品など)もありますし、故障の予兆(Potential Failure)から故障(Failure)まで(これをP-F Intervalと言います)が非常に短時間な製品では、この方法で故障前に交換を行うことは技術的に難しいためです。
ヨーロッパの場合
ヨーロッパでも、安全に関わるものは故障前に交換しよう、という考え方は日本と同じです。イメージ的に図1に示します。考え方は同じではありますが、その判断基準に対する重みづけについてはかなり違います。
図1は、ある製品についてどのようなメンテナンス戦略を取るべきかを示したフロー図です。
この考え方は「Reliability Centered Maintenance(RCM)」と呼ばれるもので、 IEC60300-3-11:2019 Reliability centered maintenanceに由来しています。
ここではその概略だけ示していますので、ご興味のある方は原本をお調べ下さい。
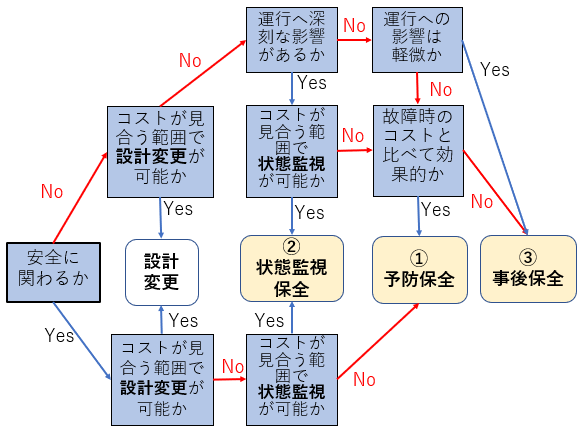
図1において、安全性に関わるコンポーネントのメンテナンスにB事後保全
(CM:corrective maintenance)・故障してからメンテする、は選択されないようになっていることを示しています。
日欧の比較
前述の図1の中の「コスト」なのですが、日本では鉄道を利用する旅客数が非常に多いことから、多少メンテナンスコストが高くなっても、列車が立ち往生することによって生じる営業上の損失が非常に高額ですので、十分ペイします。つまりメンテナンスにコストをかける選択となります。
一方欧州ではコスト次第でメンテナンス費用の少ない選択肢が選択されるため、予防保全のような高くつくメンテナンスは選ばれない傾向となります。
メンテナンスレベルとLCC
欧州では、メンテナンスの作業の複雑さによって5段階にレベル分けをしています。話はそれますが、こういうレベル分けのような概念整理は欧州ではうまいです。これなら、会社によって中身が少し違っていても、「レベルとしては同じ」、と考えられるようになるため、関連する様々な標準化が進みますので。
このレベルによってどのくらいの技能者が行うべきか、というメンテナンス計画や、メンテナンスを外注するか内部で行うか、という判断材料になっています(欧州規格のEN 13306で用語定義しています)。
そんなレベル分けをしなくても鉄道事業者ならすぐわかりそうな話・・なのですが、このレベル分けをして類型化することにより、メーカーが鉄道製品を製造する際に、その製品がこの後どのくらいのコストがかかるか、という計算(Lifecycle costing)を行うために利用されている点が日本との大きな相違点です。
この点、詳しくはRQMS(ISO 22163:2023)に関するUNILIFEという計算ソフトについてのところで後述しますが、LCCの算出・提出は鉄道製品を購入したい鉄道事業者から強い要求として出されますので、日本・欧州メーカーとも、鉄道事業者ではないのでその算出には苦労しているのですが、欧州のメーカーは、算出に必要なデータを収拾(UNIDATAというデータベースになっています)することでこれを合理的に計算する手法を編み出しています。
例えば、EN 13306でのmaintenance level1は、簡単な動作で最小限の訓練で実施できる作業、というように規定されています。
本来複雑なメンテナンス作業(しかも会社によって異なる)も、レベル分けすることによって、あるコンポーネントが「メンテナンスレベル1」で1週間に1回、「車庫(2nd line)」で行うメンテナンスがある場合には、LCCはいくらだ、という算出ができる仕掛けになっています。
まとめ
メンテナンスの種類を決める戦略(方針)である、Reliability Centered Maintenance(RCM)という考え方を紹介しました。
この考え方自体は日本・欧州ともそう変わりませんが、日本では、故障時に生じるコストを考慮すると、メンテナンスに多額の費用をかけても十分元が取れ、欧州ではメンテナンスの費用対効果がシビアであることを申し上げました。
製品リリース時のライフサイクルコスティング(LCC)においてもメンテナンスコスト(検査コストも)が考慮されることも申し上げました。