次に進む
1つ戻る
- 1.パンタグラフ
- 2.車両の外寸
- 3.鉄道車両の軸重と材質
- 4.車体外側の標示
- 5.ETCS(列車運行システム)
- 6.オーバーラップと信号の変化
- 7.連結装置
- 8.脱出窓
- 9.レールの接地/非接地
- 10.ATCの速度照査パターンの引き方
- 11.電磁吸着ブレーキ
- 12.分岐器の鎖錠
- 13.デジタルモデリング・BIM・UICリーフレット
- 14.軌道構造
- 15.軌道構造・人材育成
- 16.接着・溶接認証
- 17.「速度信号」「予告信号」が必要な理由
- 18.速度超過検出
- 19.異相区分切替セクション
- 20.波動伝搬速度[架線の張力]
- 21.サードレールの活用
- 22.車両材料による火災対策
- 23.鉄道運転免許
- 24.プラットホームの高さ・ドア高さとドアの大きさ
- 25.車両のドア構造
- 26.5G対応無線式信号(FRMCS)
- 27.高速鉄道線のトンネルの断面積
- 28.列車の分類
- 29.民営化された国鉄路線(工事中)
- 30.行路表の配布者
- 31.オープンアクセスは強制開放
- 32.客室の座席配置
- 33.列車位置把握(工事中)
- 34.高速鉄道の在来線線路走行
- 35.メンテナンス
- 36.車両の堅牢さ
- .まとめてみました
目次
溶接認証・接着認証
見えない部分の管理
新たな素材の取付品質確保
JR東日本さんのE231系電車等、ステンレス鋼製の車体前面部に白い(※最近は下の写真のように灰色)もありますが、FRP(ガラス繊維強化プラスチック)製のカバーで覆う構造や、あるいは、ポリカーボネート製の大きな窓をもつ特急車両等、異種材料を組み合わせる車両が増えています。
樹脂系の材料は金属より軽量で腐食に強く、ある程度の強度があることから様々な部位に新しい素材の採用が進んでいます。大きな窓など斬新で、以前ならコスト面で採用できないようなデザインも取り入れられるようになったのも樹脂系の材料のおかげといえます。
このような新しい素材との異種材料間の結合のためには、新しい技術が開発されるとともに、その品質確保のために従来と異なるアプローチが採用されています。
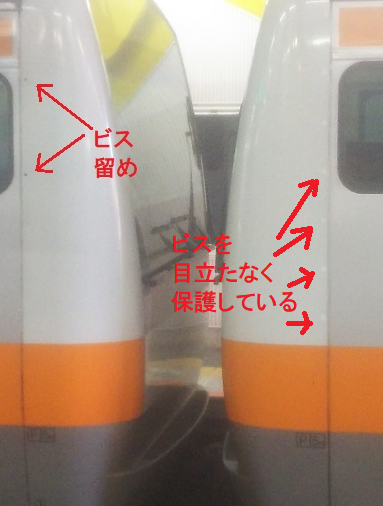
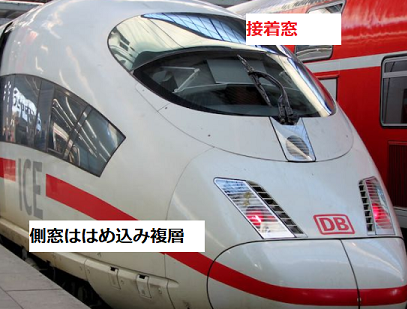
日本でも、下の写真のような通勤車両の側扉の窓は接着で取り付けています。接着したものは取付状況の検査が難しいため、社内での技能試験等、作業者の資質によって品質を確保しています。
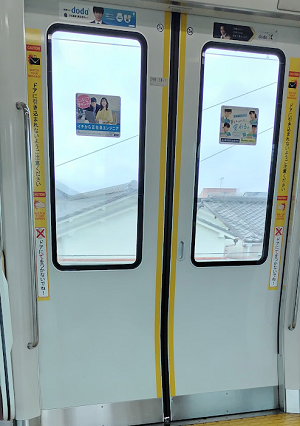
接着認証
軽量のFRP等の樹脂系の素材は溶接ができませんので、E231系のFRPの場合にはビス止めをしています。ですが、自動車や海外ではFRPのような樹脂系材料は軽いため、接着剤によって十分な接着強度が得られるとして接着剤で接着する工法(structual bonding technology)が採用されています。接着ができることで、デザインの幅が広がるそうです。
接着自体は日本でも、客室床材や内装材、屋根の不燃材、防水等のシール材、上述のドアの窓等には接着が使われています。でも、2010年ごろから欧州や中国の車両で見られるのは、車両の軽量化のために金属製のものから樹脂系の材料に切り替えた上で、従来であればねじ止めしていたような車両前面ガラスや、床下機器の保護カバー、配管等を面的に接着することが行われている点です。これによって車両の軽量化と、金属より腐食に強いという素材の利点を生かすことで、コスト減と意匠性を増すようです。また、ちょっと違う用途ですが、パンタグラフのすり板も、欧州では接着剤によって接合されています。
接着についての規格化の考え方について触れたいと思います。材料同士を安全に固定するためには、その場所に想定される加重に耐えられる力で接着されなければなりませんよね?
同じ接着剤を同じように使用しても結果に差が生じる(=接着工程の管理が品質に影響)という特徴が接着剤にはあるので、接着を確実に実施するためには、形状等の設計を工夫(=構造接着といいます)をするとともに、接着剤の選定、接着場所、接着技能、接着の工程を管理する、というアプローチにより規格化が行われています。
日本でも自動車メーカーさんが独自の規格を制定していますが、現状(2021年)では以下のようなドイツ工業規格が鉄道について制定され、適用される場合があるため、有資格者を増やしているところです。
- DIN 2304:2020 接着剤接合プロセスの品質要件 ※全産業向け
- DIN 6701-1:2004 鉄道車両及び部品の接着剤による接着-パート1:用語と基本原則
- DIN 6701-2:2015 鉄道車両及び部品の接着剤による接着-パート2:接着剤で接着された部材のメーカーの資格
- DIN 6701-3:2015 鉄道車両及び部品の接着剤による接着-パート3:設計と確認(verification)
- DIN 6701-4:2015 鉄道車両及び部品の接着剤による接着-パート4:製造工程管理と品質管理
日本国内ではこの規格への適合性が要求されることは現状ではありませんが、欧州系メーカーから部品メーカーにはこの認証対応が求められる場合があるため、欧州規格欧州系メーカーに納入する日本の電機メーカーさん等ではこの認証に基づく以下のような有資格者を社内に育成し確保する動きが進んでいます。
- European Adhesive Bonder (EAB)・・ボンダー(技師)
- European Adhesive Specialist (EAS)・・接着スペシャリスト(監督者)
- European Adhesive Engineer (EAE)・・接着エンジニア(責任者)
溶接認証
日本のメーカーさんで輸出に大変苦労するものをアンケートをとると、ここで紹介したいEN15085(溶接)か、後ほど紹介するEN45545(火災対応)、EN 15227+A1(衝突安全性)は必ず挙がります。
EN15085については、日本の規格には無い、溶接管理技術者や管理組織、試験方法(ISO17662を引用)、品質管理等の要求があるためなのですが、EN 45545も、EN 15085も、リスク発生源により手厚く対応しようという考え方で運用される場合がありますので、その観点から紹介したいと思います。
大小さまざまな金属材料が使われる鉄道車両には、多くの溶接が使われます。
溶接個所数が多いと工数が増えるため、例えば床下の吊溝(床下機器箱を吊り下げるための金具)を押出成形で製作するなどの工夫も行われています。
また溶接時の熱によって金属の歪み(残留応力)が残る場合や、寸法が公差(許容されている誤差)に収まらなくなる等の不具合が生じるため、溶接方法については溶接する間隔や使用治具、肉厚等の条件等、詳細が規格やガイドラインによって標準化されています。
- JIS E 4047 鉄道車両−旅客車用構体−溶接継手設計方法
- JIS E 4048 鉄道車両−旅客車用構体−スポット溶接継手の設計方法
- JRIS R 0142 ステンレス鋼製車両用構体部材
日本規格(鉄道関係)
- EN 15085-1:2007(+A1:2013) 鉄道分野−鉄道車両及び機器の溶接−第1部:通則
- EN 15085-2:2020 鉄道分野−鉄道車両及び機器の溶接−第2部:溶接業者の品質要件及び認定
- EN 15085-3:2007 鉄道分野−鉄道車両及び機器の溶接−第3部:設計要件
- EN 15085-4:2007 鉄道分野−鉄道車両及び機器の溶接−第4部:生産要件
- EN 15085-5:2007 鉄道分野−鉄道車両及び機器の溶接−第5部:検査、試験及び文書化
欧州規格
ここでは省略しますが、溶接については「EN 13749(台車枠の構造要件を指定する方法)」、「UIC 515-4(客車構造)」、「 UIC 615-4(台車枠構造)」など部位別に定められた設計規格や、車体の強度要求・試験(EN15227,13749 )などと密接に関係しています。
溶接に関する欧州規格のうち、EN 15085-1〜-5については、欧州の車両 TSI(4.2.2.4、AppendixD)において車両の溶接に適用するように2019年の改正で義務化されています(リンク先は2019年の改正法です。改正により全シリーズを適用することが明確化されました)。
一方日本において、日本のJISや日本鉄道車輌工業会規格(JRIS)については法的には義務づけられてはいませんが、基本的には適用されていますし、各メーカーさんが定めている設計・施工標準もこれらに沿って制定されていますけれど、ENとJISではスコープ(規格の対象)がまったく異なっており、欧州規格(EN)では以下のように必要となる溶接の品質や、その認定についても定める広範な内容となっております。特に、試験方法が決められていることや認証制度が入っていることが大きな違いです。
一方、米国ではAWSという別の体系の溶接規格があるため、北米向けはAWSがほぼ必須に必要で、欧州や欧州のTSIが参照されている地域ではEN15085が必要、・・と、輸出対象国に応じていくつもの認証が必要であり、認証取得・維持コストが必要になります。
こうしたコストはいわば二重投資ですから、どれかに統一できればよいのですが、相手がある話ですし、溶接部位の試験方法は日本も、米国も、欧州も今までの方法を変えたくない(←変えることにリスクがあるため)から、日本のメーカーさんでは納入先によって、国内向けの溶接方法と、海外向けの溶接管理方法と、それぞれに対応できる体制を維持しなければならない状態となっています。
ところで欧州の溶接規格のうち、EN15085-2:2007(鉄道車両・部品の溶接(旧規格))は、2020年10月に改訂されています。
この15085-2では、部品が使用される場所の安全性の度合により、Classification Level(品質要求レベル:CL)CL1〜CL3に分類します。
改訂前のEN15085-2では、ブレーキや台車のような安全に直結する場所の部品は「CL1」、内装材のような安全にかかわりにくいものが「CL4」・・のように改訂前は場所に基づいて4段階に分類していたのですが、
改訂後のEN 15085-2:2020では、単純に使用される場所でCLを決めるのではなく、RAMS(EN50126)による安全分析(safety relevance assessment)を行った上でCLを3段階で決めるように改訂されています。
CLが決まると、CLごとに必要とされている「溶接性能等級(CP)」に基づく品質で溶接を実行する要件やことが規定されています。
前述のように、EN15085は欧州や東南アジア等のENが強い地域の車両や車両部品では対応が必須になっている規格です。溶接技能者の認定と、溶接を行う工場の認定制度の2つがあり、一定期間ごとに更新も必要となるため能力維持も不可欠となっています。もし、EN15085に基づく溶接管理が必要な案件が、採算に見合うだけあれば問題は生じないのですが・・・?
まとめ
同じようにみえる鉄道車両・車両部品も、「溶接」のような基本技術において、欧州法及び欧州規格、米国規格の要求する認証制度等の品質管理方法と、日本の規格の対象範囲に差があります。また接着についても、いずれは認証が必須になる可能性がある現状です。
日本には溶接の技術力は十分あります。国内の溶接技能コンテストでは名だたる自動車メーカーの熟練者を押さえて優勝したりしている程で、技術力は問題がありません。問題は、欧州規格に適合するために必要な人材育成に時間とコストがかかる点です。
鉄道プロジェクトの仕様書を作成される方におかれては、溶接品質や台車構造・試験について、何も書かない訳にいかないため、EN15085やEN
13749(台車枠の構造要件・試験)を書かれるのだと思いますが、対応できるメーカーがあるかを確認の上で記載をお願いしたいのですが、・・・そんなこと、厳しいですよね。
正攻法としては海外の高速鉄道案件が具体化してくる前に、日本でも溶接品質について明文化しておければよいのですが・・ビッグプロジェクトでもなければそんな暇ないですよね。
5面加工機の実演(レールフェスタ in にいつ2017)
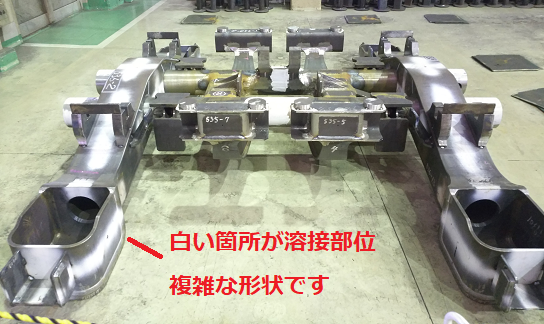
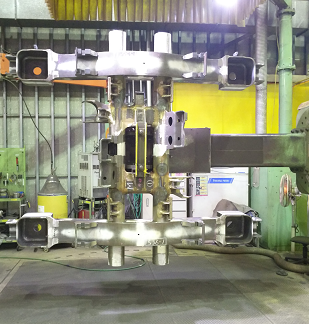